Nearly every participant in the North American oil and gas industry has heard plenty of hype about the Industrial Internet of Things (IIoT) being the panacea for domestic onshore producers. Although the current state of IIoT technology demonstrates some preliminary benefits to this industry, producers do not need to wait until these technologies are fully proven to achieve Digital Transformation. Evolutionary paths available today provide the ability to achieve desired business results while still operating within current financial and logistical constraints. The key to success in this effort is the effectiveness with which the producer’s human resources interact and leverage any given technology to deliver the benefits promised by Digital Transformation.
The current state of this industry is sometimes referred to as “Shale 3.0” where Wall Street and Private Equity expect producers to operate within cash flow. With this expectation, producers are simultaneously challenged with organizational constraints such as sufficiently skilled resources and overcoming existing technology consumption gaps. Additionally, existing infrastructure is typically a mixed bag of various technologies that are not being fully leveraged while other technologies are functional bottlenecks (ex: SCADA data management, radio connectivity/bandwidth).
Digital Transformation delivers improved employee effectiveness through their interaction with technology to achieve optimal business results. Digital Transformation focuses on:
- Automating Workflows
- Improving Decision Support
- Upskilling Workers
- Mobility (Access and Connectivity)
- Embracing Change Management
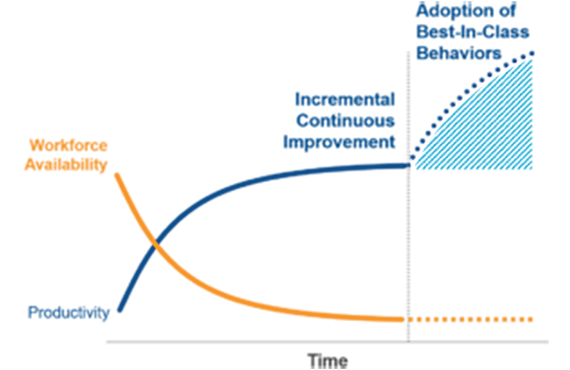
Imagine an organization that could spend less time on rote activities to focus on the higher-level problem solving. The next generation pumper could become the new “Field Analyst” with the ability to self-perform process diagnostics and analytics in the field to remediate issues. Likewise, imagine the value of the avoidance of a well workover rather than a post-mortem well review of a logged off well.
Producers have historically installed technology with mixed success. One challenge commonly seen in the industry is the technology consumption gap, where many features are available but are not being deployed and/or not achieving the promised results. In a recent discovery workshop with a producer, it was clear that the C-suite’s priority was to focus on leveraging existing investments rather than vaporware that has yet to prove its mettle. Other common challenges include training, modifying workflows, and implementing new processes.
The challenges and root causes faced by NA onshore producers are common and repeatable in each field and shared across multiple fields and operators. These challenges can be addressed by a blend of technology and work practices, in conjunction with empirical working knowledge associated with operations. Therefore, common solutions to these common issues can be productized and deployed repeatably across operating fields and producers as “killer applications” available on existing commercially available technology.
Enterprise and cloud computing coupled with artificial intelligence and machine learning has been hyped as the primary solution for Digital Transformation. That said, there is increasing recognition that a substantial amount of benefit can be achieved at the Edge and in closed loop connectivity to Level 2 SCADA and/or Cloud computing. These solutions operate real-time in the field, providing report by exception push notifications, intermittent updating of setpoints/constants, and/or uploading datasets for further higher-level analytics. Similar to closed loop process control, the concept of the “Little Loop” provides automated closed loop operation and/or operating guidance for activities that are currently being performed manually as an open loop.
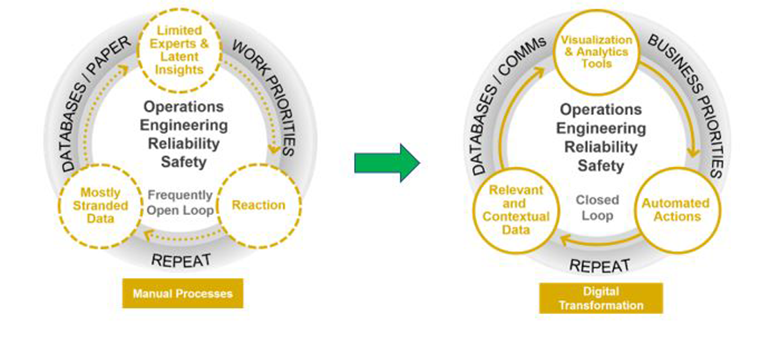
Examples illustrating the power of the Edge today include:
- Many current field devices provide more than just real-time process values. These devices contain a wealth of secondary variables and diagnostic information that provide direct data such as device health, but this data can be interpreted real-time as process analytics and in closed loop control.
- Edge computing and associated integrated Edge applications leverage information holistically to deliver incremental business results above and beyond deployment of “islands of automation”. Pad level optimization, produced fluids management, volume balancing, and manpower utilization improvements are realized, contributing to the producer’s KPIs
- Next generation radio communications and Edge gateways expand the bandwidth as well as support embedded applications for data management, visualization, and higher-level analytics and control.
Innovation in the oil and gas industry often occurs during times of constraint on the industry, whether it is product market prices, D&C/LOE costs, manpower availability, or Wall Street/Private Equity expectations. The long-term successful producer will embrace a culture of positive change management, empowerment of the employee, and the appropriate deployment of technology to meet its objectives. The good news is that the journey to Digital Transformation can be evolutionary. Instead of implementing new tech all at once, the ideal journey to Digital Transformation begins by leveraging currently installed technologies first, and then supplemented with strategic assets to deliver the remaining value desired.