One of the most common questions we receive from customers is: “What are the benefits of using a modulating pilot versus a direct spring conventional pressure relief valve?”
Emerson’s Crosby conventional spring-operated valve offers several advantages such as lower initial cost, wide chemical and high-temperature compatibility. However, Anderson Greenwood’s 400 series modulating valve incorporates an advanced design in pilot-operated valves across the industry that may be better fit for your application. The 400 series modulating pilot is equipped with a non-flowing pilot that allows for a higher operating pressure and a lower leakage rate, resulting in lower product loss. Table 1 compares key features of the modulating pilot valve versus the direct spring valve.
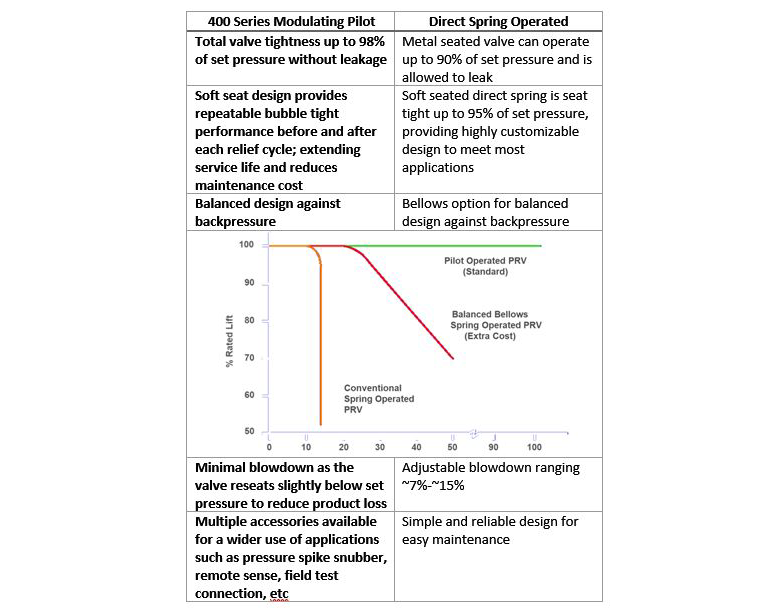
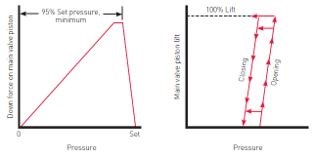
Figure 1 and Figure 2 show some of the key reasons why the 400 series pilot is able to operate closer to set pressure and why the leakage rate is reduced. In Figure 1, the graph on the left shows how the seating force increases until 95% of set pressure, creating a bubble tight seal. The graph on the right shows how the valve opens as the pressure increases until 8% above set pressure when the valve reaches full lift. Once at full lift and the pressure begins to decrease, the valve reseats slightly below set pressure. This modulating effect minimizes the amount of product loss.
Compared to Figure 1’s conventional spring operated valve, Figure 2’s graph on the left shows how the seating force decreases when approaching set pressure, allowing the valve to simmer. This is opposite to how the 400 series valve operates where the seating force increases when approaching set pressure, allowing for a bubble tight surface closer to the set pressure. The graph on the right illustrates that the spring-operated valve begins to open at 90% of set pressure and continues to open based on the percentage of lift capacity as the pressure increases. Ultimately, the direct spring valve reaches full lift, relieves, and reseats approximately 7-15% below set pressure.
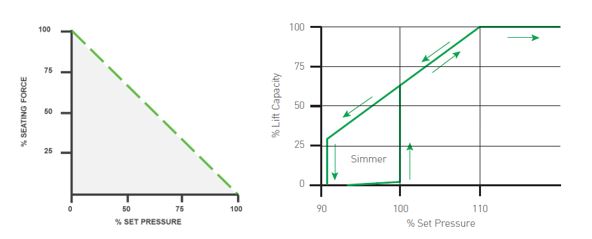
Table 2 below compares the estimated cost of ownership of these two products. As you can see, the installed cost is higher for the pilot valve, however the total cost of ownership is less over time when taking repair costs and product loss into consideration.
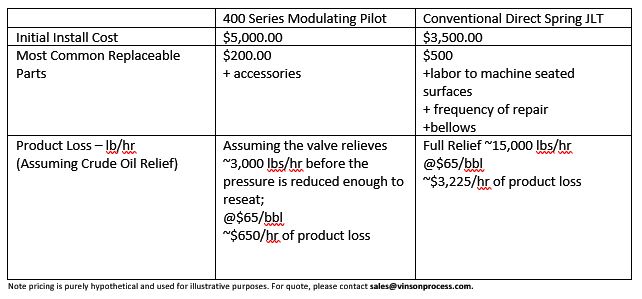
As can be heard in the video below, the modulating pilot begins to relieve once inlet pressure reaches set pressure, and continues to relieve gradually as the inlet pressure rises above set pressure. Responding to the system pressure, the relief is proportional to the process upset and will reseat slightly below set pressure in order to minimize product loss.
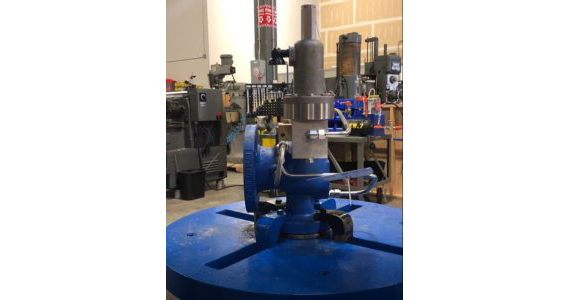
The Anderson Greenwood 400 Series pilot operated valve offers many key benefits to reduce product loss, reduce emissions, and extend service life for gas or liquid service. Pilot operated relief valves should be considered as a reliable alternative to a conventional spring valve in a variety of applications, such as liquid relief to minimize the destructive effects of “liquid hammer” or in services with emissions requirements.
Please contact Vinson Process Controls at [email protected] to learn more or to request a quote!